above> 1 inch collection
we’re talking to london designer jasper morrison and the evolution of his chair, 1 inch. we’re in the emeco showroom. some of the questions have been edited for brevity and clarity.
[DesignApplause] jasper, is the new 1 inch collection better or just another?
[jasper morrison] big smile – it’s always better. that’s the goal. to get better. and working with emeco, especially with emeco, where only one product is shown every year…the goal is to look towards the future creating products which are natural descendants of the original.
we looked at emeco’s whole catalogue and tried to find the gap. we found the gap to be a more comfortable, better-looking stacking chair and how could we make this a slightly cheaper price point than the usual emeco chair. we wanted to stick with a square tube to keep the emeco language going, but maybe we could replace the welded seat back with a plastic option. maybe it would sort of enrich it a bit because you have this fantastic recycled material that allows us to work with a new shape, a square tube.
[DA] gregg (buchbinder, ceo) was telling yesterday that 1 inch looked like a very simple solution, but it turned out not to be so simple.
[JM] it was a hell of a lot of work. when you bend a round tube, you can imagine that whatever direction you bend it in, it bends the same. but when you try for curves which are going in different directions with a square tube, it doesn’t like it. it’s very difficult. particularly the top where it can buckle the whole thing. so we had to redraw it many times. the factory would try and do it and each iteration it was bad news again, that the square was not liking to bend that way.
[DA] were you getting worried?
[JM] yes. and then, slowly we got to something better in the last minute and we were able to show prototypes in milan (2017). now we’re working on perfecting them.
[DA] this all sounds very technical and innovative. was there an ‘aha’ moment?
[JM] there were many ‘oh no’ moments. it was much more slow. it went on through the whole year, really. i think we can be fairly sure that there won’t be too many copies. don’t think anybody would have the patience.
[DA] when did this project begin?
[JM] we started before milan 2016. we only had fifteen months. some of that was for the design. we didn’t get the first prototype until after milan last year. but now we have a collection featuring a chair and armchair, stools in three heights, and café and bar tables.
[DA] gregg also made mention that 1 inch represents emeco’s first stab utilizing upholstery. how did that happen?
[JM] emeco is very unctuous of what people ask for. after so many years of aluminum it soon became clear that we needed plastic and wood. now we need upholstery too.
[DA] you’ve made very hard materials look soft with 1 inch. the upholstery makes things even softer and is unusual, i can’t describe the feeling. not sure if it’s foam or air. what is it?
above> 1 inch collection | emeco | 2017
[JM] we’re using the original seat itself and plopping upholstery and foam on top of it. you know very well if you sit on something flat, it’s not very comfortable. you sit on something curved, it gets better. if you add a little bit of upholstery to something curved, it improves again. we use very little upholstery to make it a comfortable chair.
[DA] i wanted to talk a bit about the process as well. does your design process drive the solution or is the problem driving the process?
[JM] with both this project and the previous one shown the year before, we do it really by conversation. with the first chair i’m asking a lot of questions like: how could we make a more affordable emeco chair with the material and supplies they already have. are there limitations, things we can’t do without losing quality while using recycled materials? the 1 inch frames are recycled aluminum and the seats are 100% reclaimed wood polypropylene, sustainable plywood or upholstered.
for me, before i start the design, it’s much easier as a designer to talk your way into a project than to sit down with a piece of paper and then say voila! then give your paper to the manager. i like designing by discussion with the players, the team thing, you know? a project doesn’t happen without the company, structure, and the engineers. usually the result is very different from the one which was drawn from the beginning.
[DA] a good designer needs a good client.
[JM] absolutely.
[DA] how do you interface with the team?
[JM] this project provides an interesting example. one member from our team in london was just at the emeco factory for three days. up till that point no one from our office had a face-to-face with emeco’s factory. we were just wiring 3d drawings back and forth. once we got through the milan thing, we decided they should meet and gregg flew him over. he arrived with all these templates to make it happen and had their first very physical discussion about what shape the chair should be.
[DA] are you computer savvy or are you still a sketcher?
above > alfi shell drawing | emeco | 2015
[JM] i’m still stuck on the 2d program. i pay other people to do the clever bit. i have sent sketches occasionally to start a project, but not usually. i usually do a precise 2d drawing that is the basis for the first 2d digital. after we make a few 2d adjustments we then go 3d and i can then spin it around and check it from every angle. typically i’ll put the old one beside the new one. there’s quite few back and forth making adjustments. but i don’t need to do any more drawings after the first one.
[DA] what’s the prototype stage like?
[JM] the first prototype is quite tiny. the next one we can probably sit on and we begin making functional adjustments. (we’re sitting on prototypes during our chat and jasper says to me…) ‘is the armrest high enough?’ i see you leaning. we’re thinking about raising it up a bit.’
[DA] i am, but maybe it depends on who’s sitting in the chair. the thing is, i’m really interested in what we’re seeing, but i’m not very conscious of the chair. and are you watching everyone who sits in the chair during this prototype stage?
[JM] that’s good about taking the chair itself out of the equation. and yes, by now we have probably twenty other 3d examples of chairs and we know how comfortable each is. like the alfi chair, it’s one of the most comfortable we’ve ever done.
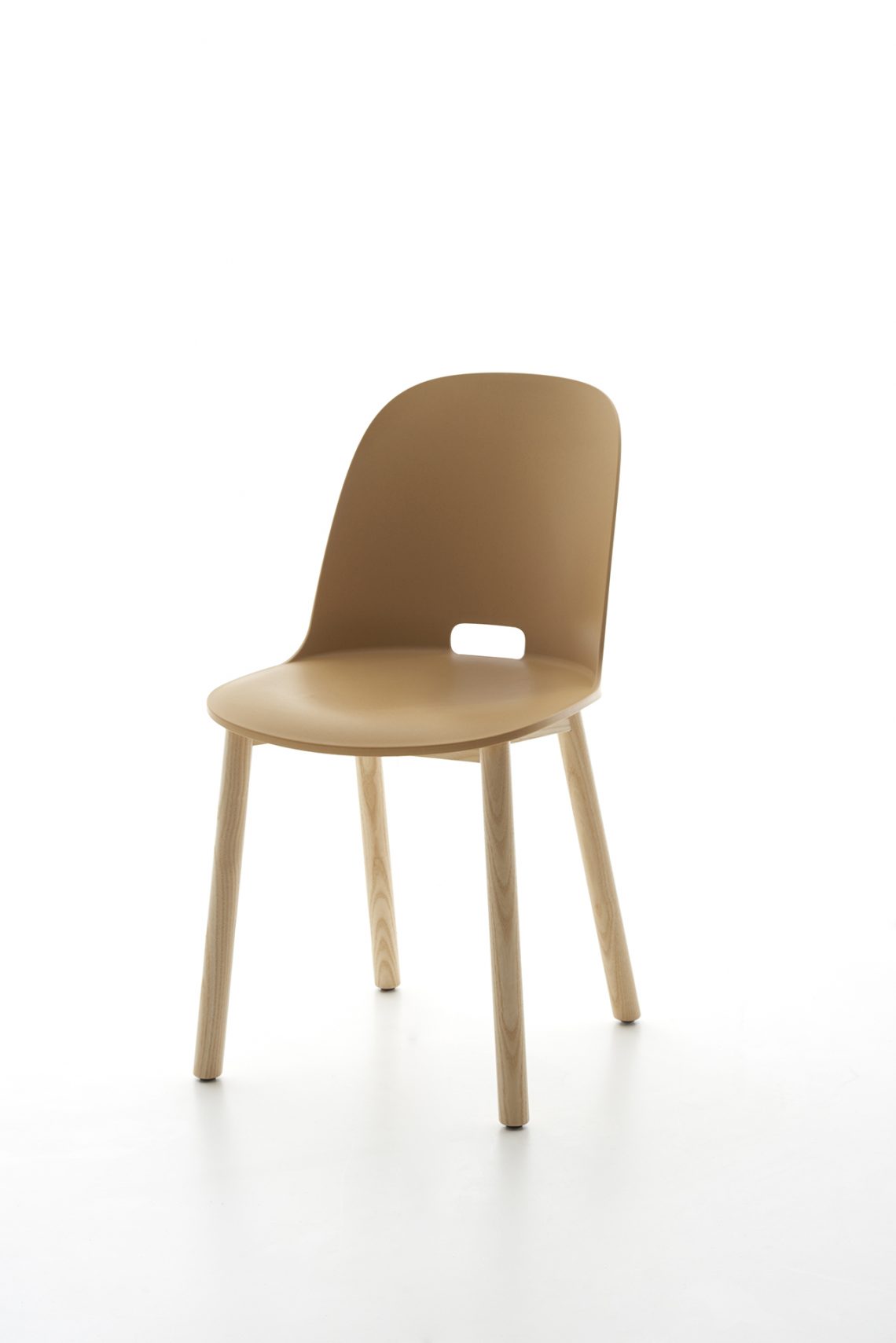
above> alfi | 2015
[DA] let’s switch gears if you don’t mind. what are you thinking about and where are you in this point in time? whether personal or professional? are some things bothering you? tell us a bit about what’s going on up there.
[JM] ok. well i’m beginning to feel a bit senior in the business. it happens. and that’s ok. i’m quite liking it. i have a fairly controlled intake of work. i’m trying not to do too much. i’m really happy working with emeco because of gregg’s paired down vision of what a company needs to be. one product a year. lots of discussion. trying to do things very well and professionally. also his insistence on recycling materials and sustainability and longevity. it feels good. we get on really well.
on another side, i don’t know if you’ve been to my shop in london, but that’s a different kind of thing. it’s very experimental for us because we buy objects from different places and put them in the shop. anybody can come and buy them.
so having the shop has been a learning process and a hobby. we don’t need to make any money with the shop and we don’t really make any money with it. but it gives a lot to the project.
[DA] what do you mean?
[JM] it’s really nice to meet the customers. and the shop setting, it’s an interesting dynamic, we get a lot of feedback that way
[DA] alright, so you have the shop. that’s the experimental thing. anything else?
[JM] i stopped doing any teaching, but i like to do books. tomorrow night i actually have a book thing going on if you’d like to come. i’ve done three books in the last four years. one of them was on my work, one was on my photos and this one i’m launching tomorrow is on the collection of the portuguese ethnology knowledge museum, which is truly amazing. there are so many nice things which were done with nearly no facilities. things made in little villages in portugal. it’s a bit like that book architecture without architects. it’s a kind of product world version of that.
[ jasper morrison ] [ emeco ] [ emeco’s time-tested material ] [ emeco’s 77-step process ]